Occupational Safety and Health Policy
We will efficiently and effectively promote both basic safety and health activities (especially those aimed at achieving zero occupational accidents and creating appropriate work environments) and Health and Productivity Management measures to maintain and enhance the health of employees. By doing so, we aim to protect the safety, security, and physical and mental health of all workers, create rewarding work environments, and continuously enhance the well-being of our employees.
Organizational Structure
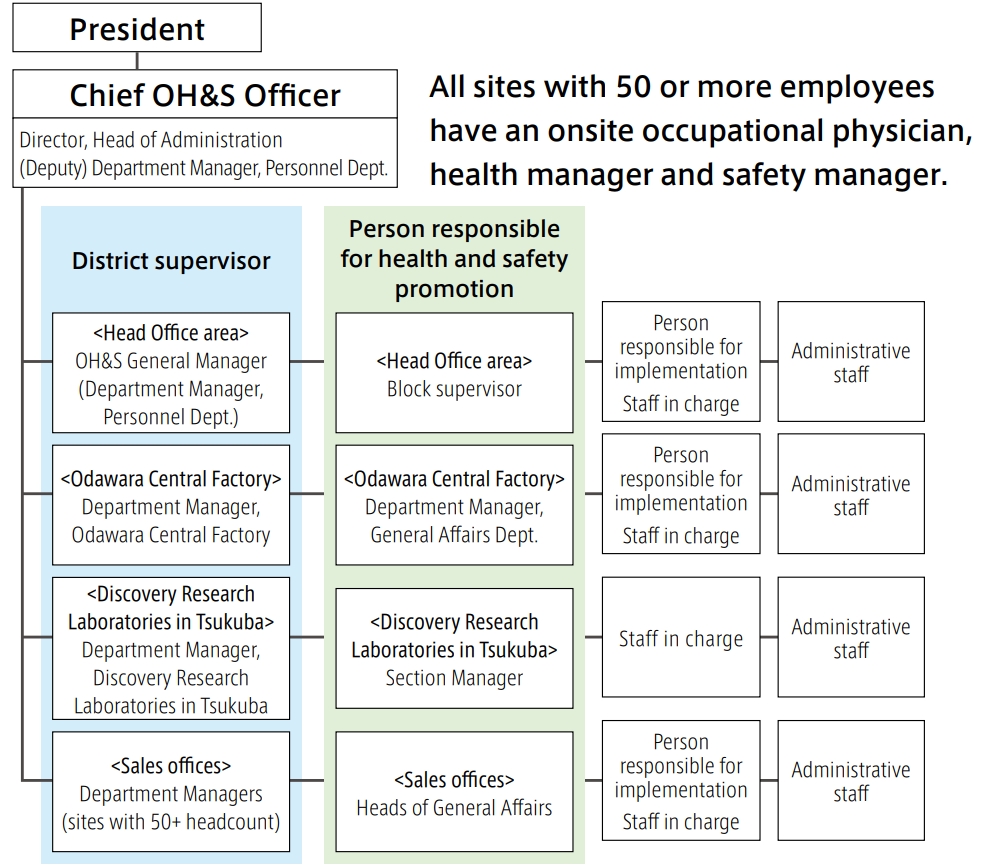
Targets
- 1. Each fiscal year, zero fatal occupational accidents and zero occupational accidents that cause workers to be absent from work for four or more days
- 2. Decreasing the occupational accident frequency rate year on year
Goals of the FY2024 OH&S focus activities
(1) Focus activity goal concerning individual employees
Encouraging employees to develop the habit of checking their health in daily life
(2) Focus activity goal concerning the entire company
Using a health management system to understand the health status of employees and implement effective health measures
(3) Specific focus challenges to be tackled
- i) Further promoting well-being management
- ii) Conducting interviews with those with abnormal findings in their regular health checkups and strengthening recommendations for secondary health checkups
- iii) Strengthening measures against presenteeism (measurement, analysis, improvement measures)
- iv) Strengthening measures to reduce long working hours and overwork
- v) Continuously developing systems for autonomous chemical substance management and promoting compliance with laws and regulations
(4) Promotion of basic OH&S activities
We will continue to conduct basic OH&S activities with the aim of achieving zero occupational accidents and zero health damage, which are the fundamental goals of OH&S activities.
・ Legal compliance • Danger prediction activities
・ “5S” activities • OH&S awareness-raising activities
Number of occupational accidents

Frequency rate | Severity rate | |||||
---|---|---|---|---|---|---|
FY2021 | FY2022 | FY2023 | FY2021 | FY2022 | FY2023 | |
Nippon Shinyaku | 0.29 | 0.56 | 0.00 | 0.00 | 0.02 | 0.00 |
All-industry average in Japan (Difference from the all-industry average) |
2.09 (-1.80) |
2.06 (-1.50) |
2.14 (-2.14) |
0.09 (-0.09) |
0.09 (-0.07) |
0.09 (-0.09) |
Average in the Japanese chemical industry (Difference from the average in the Japanese chemical industry) |
1.07 (-0.78) |
1.16 (-0.60) |
1.04 (-1.04) |
0.02 (-0.02) |
0.06 (-0.04) |
0.03 (-0.03) |
(The fiscal year [FY] is from April to March of the following year.)
- * Frequency rate = Number of fatalities and injuries from occupational accidents / Total number of actual working hours × 1,000,000
- * Severity rate = Total number of work days lost / Total number of actual working hours × 1,000
- * The number of fatalities and injuries from occupational accidents that result in the loss of at least one day of work or loss of a body part or function.
Related Initiatives
Occupational health and safety activities and risk assessment
The Company-wide Occupational Health and Safety (OH&S) Committee, which comprises the OH&S Officer (director in charge) and the representative of the labor union (chairperson), meets twice a year. Moreover, the OH&S Committee of each business location meets every month and labor union branches hold labor-management meetings four times a year in order to regularly discuss issues, such as the correction of long working hours, the promotion of holiday taking, and the working environment for telework. In addition, the OH&S Committee of each factory conducts OH&S risk assessments. At our laboratories, we conduct risk assessments of chemicals that are recognized as hazardous or harmful at a certain level in line with the Industrial Safety and Health Act. We have in place a system whereby, when new manufacturing processes or new machines are introduced to our facilities, recommendations for conducting risk assessments and providing safety education for those involved in new work are issued to the relevant departments, which later report the results.
Mental Health
At Nippon Shinyaku, we believe it is essential to devise measures to effectively handle employees’ mental health issues, which can be triggered by stress in many cases. Accordingly, we have been conducting a stress level inspection covering all employees each year since 2003. In the beginning, the stress check was mainly intended to detect early signs of mental ill health and enable employees to make an early response as part of their self-care. Since 2006, it has expanded to include workplace unit-based care training programs based on organizational analysis of stress check results, with a particular focus on sites other than the Head Office. As a result, the level of responsiveness to mental health issues has improved among executives, leading to the construction of a mechanism enabling them to make early responses to personnel in poor condition.
Main initiatives
- Workplace improvement based on analysis of stress check results
- Follow-up on employees on sick leave
- Training program for work resumption
Percentage of employees who underwent a stress check
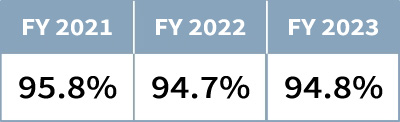
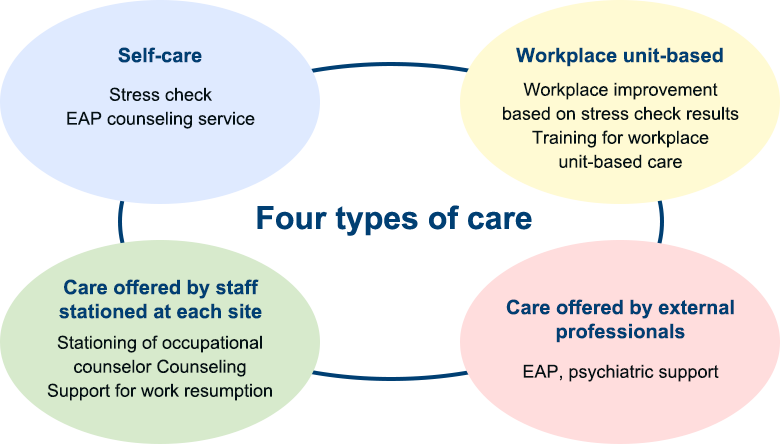
Training
The Nippon Shinyaku Group provides employees with safety and health training.
Training program | Intended participants | Frequency | Number of participants |
---|---|---|---|
Compliance Training | All employees | Once a year | About 2,400 |
Compliance training (Mental Health) | All employees | Once a year | About 2,400 |
Line Care Training | Managers | Once a year | About 400 |
Occupational Health and Safety Staff Training | Occupational health and safety staff in the Head Office area | Once a year | About 250 |
Anti-harassment measures
The Nippon Shinyaku Group recognizes harassment as a serious issue that can trample the human rights and dignity of individuals. To prevent all forms of harassment and maintain a favorable workplace environment, the Group has established Harassment Prevention Rules and a Harassment Prevention Committee and uses them appropriately. In addition, we provide our employees with compliance training and manager training focusing on harassment and train harassment consultation staff, including those at Group companies. We also conduct various awareness-raising activities throughout the year, including distributing anti-harassment awareness-raising booklets and cards to all employees and adding a harassment awareness-raising icon to the home screen of business-use mobile phones.
We have set up internal and external consultation desks dedicated to harassment as a system whereby objective decisions and prompt responses will be made in the event of a harassment case. Since harassment can cause a mental breakdown among victims, we have in place mechanisms for checking the facts and intervening in harassment cases. While even anonymous requests for consultation are accepted, we promise consultation service users that we will protect their confidentiality, as well as the confidentiality of third persons, and that we will not treat them and any third persons disadvantageously, in anticipation that the improvement of a workplace environment is likely to involve solutions to troubles between coworkers. All those working with the Nippon Shinyaku Group, including the executives and employees of Nippon Shinyaku and Group companies, as well as temporary staff, secondees, and the employees of contractors, can use this harassment consultation system.